滚珠丝杠精度失效原因分析(一)
表面损伤失效指机械零件因表面损伤而造成机械设备无法正常工作或失去精度的现象。主要包括:接触疲劳失效、磨损失效与腐蚀失效。
一、接触疲劳
滚珠丝杠副接触疲劳失效是指零件在作滚动或滚滑复合运动时,由于承受交变接触载荷,使表面材料疲劳断裂而形成点蚀或剥落的现象。具体表现有螺母、丝杠的滚道及滚珠的工作表面产生点蚀,材料产生剥落
滚珠丝杠副的材料均为多晶体。由于各晶粒位相不同,以及位错、夹杂等微观、宏观缺陷与第二相的存在,在多晶体中存在着各向异性和非均质性。疲劳破坏总是由应力应变最高和位向最不利的薄弱晶粒或夹杂等缺陷处起始,并沿着一定的结晶面开始扩展。
当滚道或滚动体的直径发生变化时,其接触线上各对应点的运动关系(旋滚比)也会随之发生变化。当滚动体直径变大时,滚子与滚道接触的对应点之间线速度不等,出现了滑动摩擦。在一定的负载条件下,丝杠副转速越高,线速度差别越大,摩擦就越强烈,并导致异常温升。
诱发滚道表面非正常磨损的另一个误差因素是:内外滚道母线和滚动体母线对其中心线的倾斜角度误差,即角度差。滚道的实际角度过大或过小,均可使载荷向丝杠副某处集中。载荷集中的区域必然是变形量和应力最大的区域。在丝杠副旋转过程中,滚道上某一点的应力随时间呈周期性变化,由0到最大值再返回到0,如此循环往复。在这种情况下,应力集中处的近表层会因疲劳而提前出现微小裂纹,这种微小裂纹在反复循环载荷下扩展,最终扩展到表层,剥落出肉眼可见的微粒,于是接触表面出现了磨损麻坑,这种现象称为“表面疲劳磨损”。剥落出的微粒又会参与到磨损当中,形成磨粒磨损,使滚道的磨损进一步加剧。
原因:长期超负荷运行;产品缺陷:如材料、硬度、滚道表面粗糙度等;润滑问题:润滑剂粘度和用量用法不当;固体颗粒侵入,循环作用造成的疲劳损坏;未及时维修或维修不当;设备老化等。措施:选择适当的滚珠丝杠产品;优化润滑方式,选择合适的润滑剂和润滑量;安装时保证零件与环境的清洁,优化密封结构;定期进行产品维护,及时更换疲劳产品。
二、磨损
材料选用优质GCr15钢。滚珠丝杠的传动功能是通过钢球在滚道内滚动时带动螺母运动的。由于一般企业采用的钢球硬度达60HRC,这就要求滚道表面的硬 必须58~63HRC,硬度太低则滚道不耐磨,硬度超过上限则会大大降低溶火硬化层的力学性能,会在滚道表面产生磨削裂纹,甚至造成丝杠断裂。对于滚珠丝杠率火硬化层深度要求,是基于丝杠耐磨性和长期反复运动的需要,为了保证其能很好地达到设计使用寿命。在对滚珠丝杠粹火硬化层组织的要求中,特别强调马氏体组织必须控制在1~4级,即隐针状马氏体,不允许出现粗针状马氏体。根据生产经验,类似滚珠丝杠这样精密的滚动轴承类产品,如果溶火组织过粗则有可能在后续的磨削加工中产生裂纹。对于滚珠丝杠表面感应溶火径跳的要求是基于两方面的原因:一是丝杠精度的要求;二是大批量产品生产的要求。在溶火过程中产生的径跳超过要求,会影响丝杠的加工精度。而且溶火后的丝杠硬度高、脆性大,校正工作难度较大,不利于产品的大批量生产,因此要求粹火时对丝杠径跳进行严格控制。
滚珠丝杠副磨损是指表面之间的相对滑动摩擦导致其工作表面金属不断磨损而产生的失效。持续的磨损使各零件逐渐损坏,并最终导致丝杠系统的精度丧失及其他相关问题。按磨损形式通常又分为磨粒磨损和粘着磨损。
(一)磨粒磨损
磨粒磨损指滚动工作表面之间挤入外来硬质颗粒或异物或金属表面磨屑相互摩擦而引起的磨损,常在工作表面造成犁沟状的擦伤或凹痕。其具体表现为丝杠系统运行剧烈颤动,有噪声;滚珠运动阻滞,螺母卡死;丝杠、螺母的滚道工作表面有不均匀凹坑,局部剥离
产生因素有:密封不合适或损坏造成金属颗粒等异物侵入;安装或工作环境不清洁,造成污染;润滑剂不合适等。措施:选择合适的密封形式,及时更换受损的密封件;改善运输、安装与使用方法和条件;选用合适润滑剂图6-2螺母滚道的凹坑并及时更换等。
(二)粘着磨损
粘着磨损指由于摩擦表面的显微凸起或异物使摩擦面受力不均,在润滑条件严重恶化时,因局部摩擦生热,造成摩擦面局部变形和材料焊合现象。轻微的粘着磨损称为擦伤,严重的粘着磨损称为咬合。具体表现为滚珠或滚道变粗糙;接触面擦伤、材料卷起
产生因素有:滚珠在进入与离开承载区域时的急剧变速;润滑剂的种类与用量不合适;异物侵入,滚珠滚动受阻;有水侵入等。措施:根据工况选用合适的丝杠产品;选用合适的润滑剂和润滑量;改善密封等。
丝杠和螺母采用相同的材料和热处理工艺,硬度基本相同。虽然螺母滚道面的工作时间比丝杠轴滚道面长,但是实践中却发现,丝杠轴的磨损明显大于螺母,致使丝杠副的有效寿命大大缩短。接触应力理论分析表明,虽然滚珠与丝杠滚道和螺母滚道的接触压力相同,但由于接触曲率不同,其接触应力存在较大差异,滚珠与丝杠滚道的接触应力要大于滚珠与螺母滚道的接触应力,接触应力的差异导致二者摩擦特性不同,这是丝杠滚道磨损较快的一个重要原因。根据弹流润滑理论计算的最小油膜厚度值表明,滚珠与丝杠滚道和螺母滚道接触副之间无显著差异,但丝杠为细长轴类零件,刚度较低,在磨削过程中由于振动会导致精磨表面的粗糙度值较高,因而其润滑状态要比螺母滚道更恶劣。另外,在高温状态下,离心力的作用可能会导致润滑油脱离丝杠滚道,造成丝杠滚道润滑状态进一步恶化。接触应力大且润滑状态差,这两者综合作用的结果导致了丝杠滚道磨损过快,影响了丝杠副的有效寿命。
三、腐蚀
摩擦副对偶表面在相对滑动过程中,表面材料与周围介质发生化学或电化学反应,并伴随机械作用而引起的材料损坏现象称为腐蚀磨损。具体表现为滚道工作表面出现不均匀的坑状锈斑或与滚珠节距相同的锈蚀,丝杠整体生锈及腐蚀(参见图6-4)。
产生因素有:存放或使用不当,水、腐蚀性物质等侵入;温差变
化大,形成冷凝水;密封失效;润滑剂、防锈剂不合适等。措施:存放与使用时禁止腐蚀性物质等侵入,能避免与水和腐蚀性物质接触;改进密封;采用抗腐蚀能力强的润滑剂;暂时不用或停转时采取正确的防锈措施。
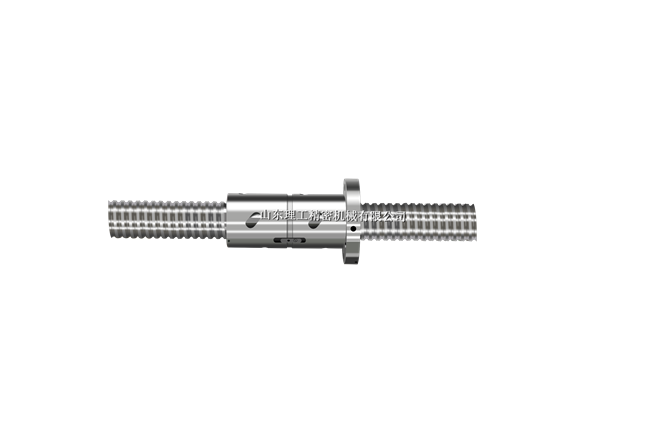
相关资讯: